The key enabler for powering the EV transition: lightweight composite battery enclosures
An energy transition is sweeping the globe. The electric vehicle (EV) industry and worldwide battery market are experiencing unprecedented growth alongside it. The lithium-ion (Li-ion) battery industry will reach over $400bn in value by 2035 according to GlobalData research, up from just under $90bn in 2022. It amounts to a robust 12.5% compound annual growth rate (CAGR). Soaring demand for clean mobility solutions is the key driver. The ascent of EVs – both passenger cars and commercial vehicles – will underpin the Li-ion battery sector’s expansion over the next decade. McKinsey forecasts that mobility applications will command at least 90% of battery demand by 2030. GlobalData’s projections are equally grand, with EV production expected to reach 17.3 million units by 2025 – 18.4% of total light vehicle production. By 2028, this figure is anticipated to escalate to 28.3 million units, accounting for 28% of production. Growth will only continue into the 2030s.
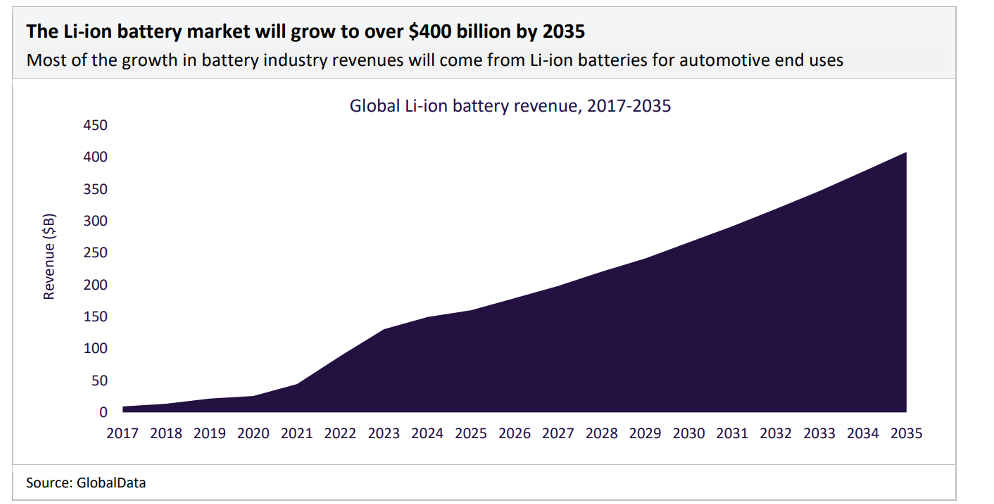
Despite significant advancements, Li-ion batteries remain bulky, hampering EV performance and efficiency. Anxieties around range also persist among potential buyers. Reducing the weight and size of battery packs while also increasing battery efficiency is paramount if these are to be overcome.
Innovative battery enclosures are emerging as an important part of the solution. “New lightweight battery enclosures can replace heavier metallic battery covers and trays typically made from steel and aluminum, with glass or carbon reinforced composites,” says John Conn, Engineering Project Manager R&D at Mitsubishi Chemical Group. “This will help offset the added weight of larger battery packs.” These enclosures offer a wide range of advantages: consolidation of components, boosted thermal safety, corrosion resistance, design flexibility and material characteristics tailored to specific needs. They offer both lighter weight compared to larger battery packs and enhanced safety, protecting the battery from external impacts from road hazards, as well as preventing battery thermal runaway or fires. As EV and battery markets continue their onward march, innovative enclosures will be a defining factor for sustained success.
Enclosures in the driver’s seat
In the quest to get new electric vehicles on the road, the type of enclosure surrounding a battery may not be at the forefront of manufacturers’ minds. But it should and must be – for a number of key reasons.
First, efficiency and lifespan. The cornerstone of a new EV battery, lightweight composite enclosures contribute to increased vehicle range by reducing energy consumption. Additionally, modern enclosures are integrated with advanced thermal management systems, ensuring batteries operate within optimal temperature ranges. This can prevent overheating and extend battery life. Modular designs facilitate easy assembly, maintenance, and repair, allowing for quick replacement of defective components without extensive disassembly. Moreover, their cutting-edge, multi-functional materials combine properties such as flame resistance and electromagnetic interference (EMI) shielding. “By incorporating multiple functions within the composite material, additional post processing steps can be eliminated. For example, if the composite material is an inherent EMI shield, a secondary processing step to apply metallic foil as an EMI shield to the part can be eliminated – which ultimately reduces costs,” says John Conn.
Second, sustainability. Innovative sustainable composite materials include those made from bio-based raw materials and bio-based fillers, both used in the making of modern battery enclosures. Additionally, at End of Life, recycling and re-use of these materials in the making of new parts aligns with sustainability directives like the EU’s End-of-Life Vehicles (ELV) Directive – promoting circular economics in the automotive sector. And incorporating recycled plastics aligns with a European Commission mandate to use at least 25% recycled plastics in new vehicles – critical given that plastics constitute an average of 50% of a car by volume. Furthermore, by reducing the vehicle’s overall weight, lightweight enclosures lead to better energy efficiency.
This leads onto a crucial third advantage of modern enclosure technology: flexibility. Composites allow design flexibility typically not afforded by traditional materials. Parts with complex geometries can be designed with material properties tailored to the application, and assemblies can be simplified resulting in parts consolidation and reduced joining operations which can increase reliability. Additionally, innovative composite materials enable OEMs to manufacture parts with fast cycle times allowing for high volume production. Also, manufacturing automation can increase production efficiencies and reduce costs. Combining optimized designs with fast cycle times and production automation can result in a significant benefit to the OEM.
The road ahead
The EV industry is accelerating towards an innovative future. As it does, advances in battery technology and enclosures will accelerate too – revolutionising the entire transportation landscape, including not just cars but also eVTOL, drones and aerospace. As we move beyond automotive applications into different EV applications such as Urban Air Mobility (UAM) including eVTOL and drones, adapting lessons learned will enable innovation and growth. For example, developing composite materials/parts for the UAM market with the fast cycles times as typically required by the automotive market, but with the high quality demanded by more stringent aerospace regulations.
Marcel Remp, Strategic Growth Manager Automotive/ Mobility at Mitsubishi Chemical Group (MCG), identifies “innovative manufacturing methods and the development of a new generation of composite materials” as a critical trend for the battery enclosure market, as the quest for fast cycle times combined with high performance and low costs ramps up. Additive manufacturing, 3D printing, nanomaterials and bio-based composites are enabling lighter, stronger, and more sustainable battery enclosures. Consider the work being done by companies on the forefront, like MCG; they work with major OEMs to deploy advanced thermoset and thermoplastic composite is contributing to changing the game in how efficient, high-performance battery enclosures are produced.
Top manufacturers have also raised sustainability as a major and growing focus for future battery enclosures. Designing with circular economy principles in mind, manufacturers are emphasizing recyclability, reusability, and resource efficiency. Closed-loop recycling processes are being implemented to recover valuable materials from end-of-life battery enclosures, which are then integrated into new products. MCG’s commitment to environmental sustainability ensures that its materials and production practices minimize waste and promote a circular economy.
Structural integration is another significant trend. As battery enclosures evolve to become integral parts of a vehicle’s structure, rigidity and crashworthiness are becoming increasingly important considerations. At MCG, the latest designs seek to integrate the battery pack into the vehicle chassis or body panels, offering significant weight savings and space optimization. In doing so, it improves vehicle efficiency and enhances safety for drivers.
And a whole host of new tech is hitting the auto industry to refine vehicle performance. Advanced sensors, monitoring systems and connectivity features are all making their way into battery enclosures to enable real-time data collection and analysis. Meanwhile, the advent of solid-state batteries, which offer higher energy density and improved safety, mean new designs for battery enclosures will continue to evolve.
Mitsubishi Chemical Group stands out by offering a comprehensive suite of solutions, addressing every aspect of battery performance and safety – those of today and tomorrow. Their portfolio of advanced materials includes a range of solutions for EV Battery Enclosures, such as: Flame-retardant fiber-reinforced thermoplastic for battery covers that have been tested per UL2596; high strength lightweight carbon fiber reinforced thermoset Forged Molding Compound and Prepregs for battery trays; phase change thermal responsive spacers and thermally conductive silicones for thermal management; and Flame-retardant PBT polymers for high voltage connectors.
This design offers significant weight savings – up to 40% versus comparable metal battery enclosures, as well as 30% smaller space requirements – improved structural integrity, and enhanced fire safety. And they use eco-friendly materials and closed-loop recycling processes to hit key sustainability targets. “We can help Tiers and OEMs meet sustainability targets from a materials perspective,” says Marcel Remp. “This means alternative energy sources for material production, bio-based materials like resins and fibers, and end of life considerations like recycling or degradability.” Altogether, it encapsulates how a market-leading battery enclosure enables an EV to be more efficient, sustainable, safe and cost-effective than ever before – essential for futureproofing manufacturers in a competitive landscape.
Companies like MCG are leading the EV charge, offering cutting-edge solutions that address the critical challenges of battery efficiency, safety, and sustainability. Fill in your details and download the whitepaper on this page to learn more about what their innovative battery enclosures could do for you.